下了订单,机械臂从仓库拿取相应部件,由AGV小车送到产线上装配、紧固,再烧录进程序……全程自动,一套根据客户需求、完全个性化定制的工业产品就此“出炉”。
同济大学工业4.0学习工厂内,记者花了几分钟就从头到尾看完了这套简短高效的流程。来上海自贸区临港新片区发展这些年来,学习工厂承接了近20项国家智能制造专项。这条自动化生产装配线,与数字孪生、设备预测性维护、远程运维等前沿技术,早已走出这个面积不大的实验室,在宝钢集团、中国电子科技集团等工业界龙头企业大展拳脚。
“前沿应用技术的科研验证、成果转化、示范,是我们的工作重心之一。”同济大学工业4.0学习工厂实验室主任陈明教授说,“人才的教育培训——尤其是工程师、技术人才的培养——是另一个重心。毕竟,这里被称为‘学习工厂’。”
最前沿技术在这里先行先试
“从下单,到出货,通过机器视觉全程精准定位、检验质量,实现全流程自动化低差错的生产。”产线正“嗡嗡”运转,陈明向记者解释它的特别之处,“但它最大的优势在于实现了‘个性化’制造。”
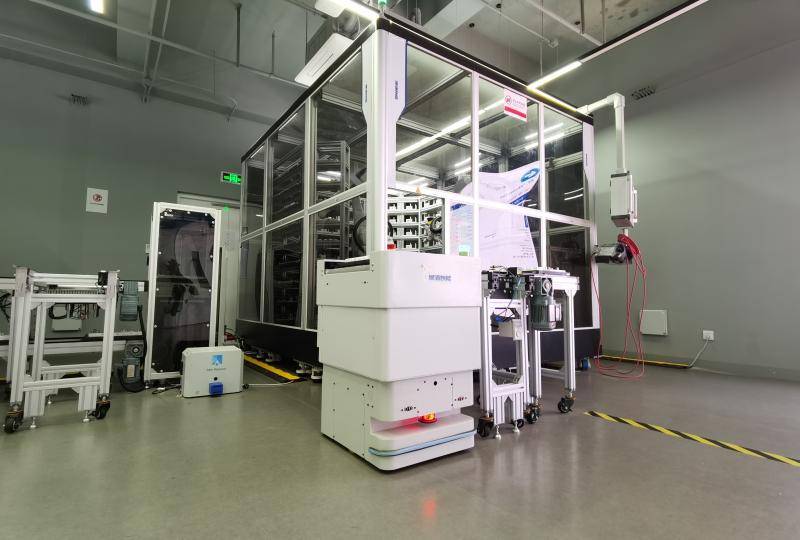
何谓“个性化”?与一般意义上的定制化、客制化不同,陈明举例,有的车企允许客户定制车辆,但也局限于是否选装天窗、选择轮毂尺寸等模块选择;而“个性化”,则能让客户自由选择每一个零件,“创造”出的每辆车都可以是独一无二的。
同济大学工业4.0学习工厂内的这条生产线,通过智能中央控制单元、智能仓储单元、装配单元、激光打标单元以及传送单元等,让个性化下单、产品智能设计成为现实。“装配哪种零部件、安装多少,这些都能按客户不同需求生产。甚至,客户提出功能需求,生产线还能自动设计。”陈明说,“比如,客户需要消防相关的产品,生产线就能做出判断——要安装烟雾、温度传感器。”
陈明觉得,随着生产力发展、技术进步与社会变迁,个性定制的需求将越来越强。届时,能够自行运转的智能工厂将成为主流。“工业界还做不到的场景,在我们学习工厂先行先试。技术成熟后,等需求跟上,就能直接投入大规模应用。”
生产设备总会磨损、故障,而越高级的设备,维护起来越难。术业有专攻,工厂里的工程师清楚设备的使用方法,却不知道怎么修。出了问题,动辄不远千里请来懂行的专家,麻烦不说,效率也低下。学习工厂研发的“远程运维”技术,就能完美地解决这个问题。
陈明给了记者一个AR(增强现实)眼镜,戴上后,再看刚才那条生产线,大量参数跃入眼帘,一一对应不同零部件。陈明介绍,学习工厂研发的远程维护系统,通过AR或VR(虚拟现实)眼镜与摄像头的配合,工程师可以将自己所见实时传输给线上的专家“联合会诊”。找出问题后,专家再将指令传回眼镜。
“哪个部件出问题、应该怎么修,都能通过图像标识‘手把手’引导工程师一步步进行。稍微具备一些工业基础技能的人,完全可以在专家远程指引下,解决绝大部分的设备维护问题。”
神奇的“双胞胎”模糊现实与虚拟的边界
远程运维系统与另一项技术“数字孪生”息息相关。陈明将其称为“数字双胞胎”,叫法更接地气,也更好懂。通过精准建模与机理仿真,它将真实世界中的机械设备完整地映射在虚拟世界中。
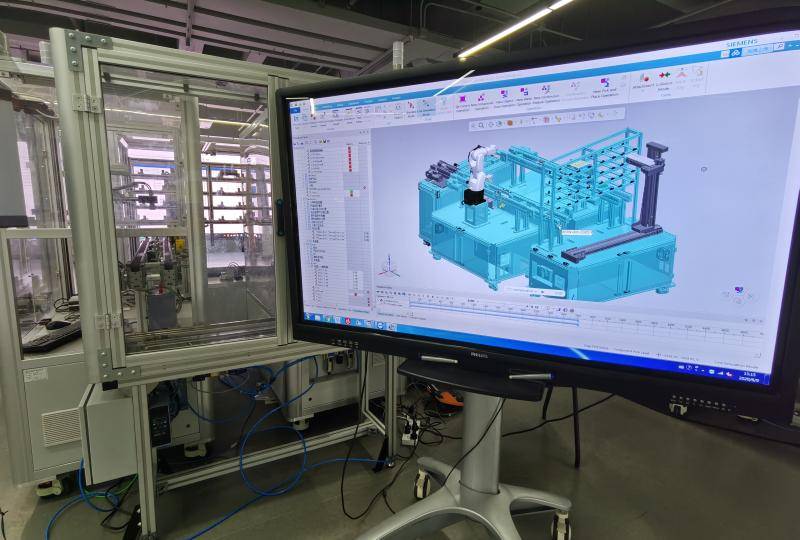
“机械运转的所有相关数据在软件中实时显示,哪个轴承磨损到什么程度——这类‘健康状态’一目了然。”陈明说,“它还能通过大量数据拟合出一条健康预测曲线,在机械真正出问题前,提醒工程师对特定部件提前维护。”如此一来,机械不用再进行定期全面检查维护,也不会在运行过程中突然损坏造成损失,精准、高效而安全。
数字孪生系统的难点在于建模。在虚拟世界中再造一个一模一样的机械,还要模拟机械在真实世界各种因素影响下的所有细微变化,这需要极高的精度与高度仿真的机理引擎。陈明介绍,学习工厂的这套系统还处于初级阶段,正在进一步优化。等技术完全成熟后,将在许多领域起到关键作用。
“双胞胎”间的映射是双向的。在软件中键入一个指令,虚拟世界中的机械“听令行事”,现实世界中的机械也会“有样学样”。一些试验可以放在虚拟世界先行尝试,确认可行后再实际操作。
这也让它成为了同济大学工业4.0学习工厂培养技术人才的一大法宝。陈明说,工科学生到工厂实习,感受真实的生产环境,是走出校门前的重要环节。但在一般的工厂,学生的重心无法完全放在“学习”上。而在这里,产线支持重复操作,系统可灵活拓展,学员有机会独立编程,引导工业机器人工作,并测试机器人与上下游生产线的配合程度;数字孪生系统还能在虚拟世界中模拟出各种场景,供学生钻研学习。
目前,学习工厂已开发8门课程,通过综合性开放式的课程设计,在实际工程环境下全面培养、提高学生的工程素养和工程能力及团队协作、组织协调能力。以往,同济大学的学生们都会集中坐大巴来临港学习;学习工厂还与海洋大学、海事大学、上海电机学院等几所临港的大学合作设立了教学基地。由于疫情的影响,学校还没开学,线下教学开展受阻,基于数字孪生系统的教学、试验却不受影响。陈明觉得,自己找到了培养学生的新方向,而他也正在同学习工厂的团队一起,对数字孪生系统进行轻量化改造,让程序得以在一般的家用电脑上顺利运行,更多学生在家也能使用系统学习。
“工科知识,最终还是要应用的”
记者采访时看到,学习工厂的所有会议室都被占满,人们正激烈地讨论技术问题,宛如身处大学校园内。陈明告诉记者,这其中不只有学生、教师,还有许多专门聘来的工程师,“教师与工程师的思维模式是互补的。工程师善于解决实际问题,而教师则能将解决的过程抽象出来,形成可复制推广的经验。要培养‘工程师人才’,两者都不可或缺。”
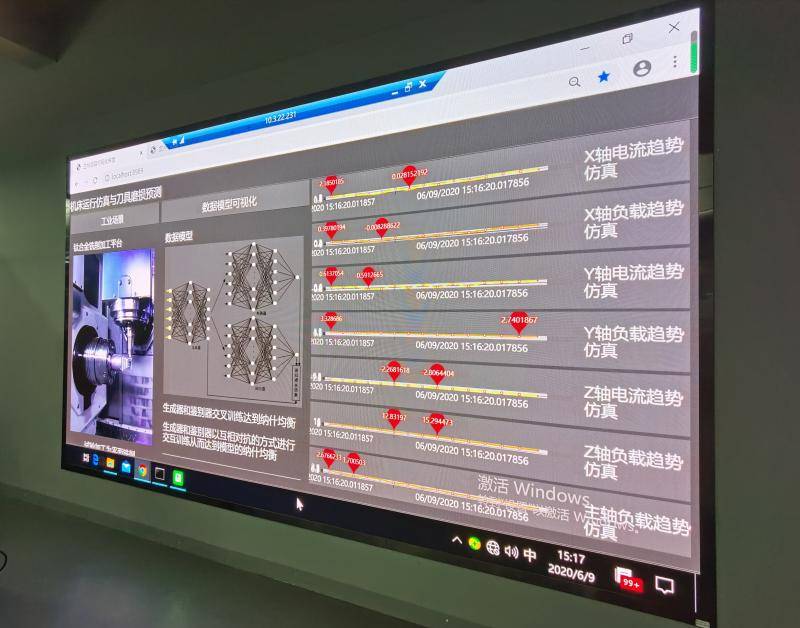
“工程师人才”,正是陈明反复强调的培养目标。他觉得,国内工科教育偏向理论,连教育者自身大多数都是“从校园到校园”,更长于学术理论研究。说到此处,他不好意思地笑了:“连我自己也是,毕业后就在学校里做研究。后来与工业界合作了不少项目,才慢慢培养起自己的工程素养。”
“科技不断进步,要学的知识越来越多,许多应用还需要工业软件、自动化等跨学科的知识。按部就班地系统学习的话,就算本科加到6年、研究生再多读几年,也很难学完。”陈明说,“学了的知识用不到,要用的知识学得不够深,是当前许多学生都会遇到的问题。”因而,他觉得,比起直接教授学生知识,教师更应教会学生如何获取知识、重构知识并应用于解决问题,即授学生以“渔”。
目前,陈明正着手推动“访问工程师”项目,让大学教师到工业界企业轮转一两年,让教师也具备一定的工程师思维,“工科知识,最终还是要应用的。以前强调学习系统知识,现在观念正在逐渐转变,更强调解决问题的能力。”在大学课程设置上,同济大学的工程本科教学也按国际本科工程学历资格互认协议《华盛顿协议》要求,向应用靠拢。教学大纲中提出要让学生拥有的每一项应用能力,在课程设置、教案乃至课后作业中都有所对应。
重视应用的思路,来自工业4.0理念发源地德国。同济大学工业4.0学习工厂学习德国工业人才培养模式,得到了国际知名认证机构德国莱茵TÜV集团的认可。去年9月,中国首个“工业4.0工程师认证考核中心”正式落户这里。陈明还在开展职业技术人才认证,机械工业职业技能指导中心也将落在学习工厂。他告诉记者,工业人才的职业认证,“德国在世界上首屈一指”。中德之间实现互认,意义非凡。
“以前,中国的工程师证书在国外不被认可。中国公司在国际上承接的项目,最终还要请国外的注册认证工程师签字,白白浪费一笔钱。有了中德互认体系,这样的情况将大大减少。”陈明说,“此外,有了这样高含金量的证书,还能吸引更多人投身智能制造行业,对行业吸引人才有着更为深远的意义。”
来临港,来对了
“2011年,德国率先提出工业4.0理念,并于2013年上升为国家战略。工业4.0带来的智能制造是连接、是集成、是数据、是创新,或是转型;所需要的并不仅是设备的升级或单纯的人工智能开发,而是要依靠信息化、物联网技术,对整个制造行业进行水平整合和垂直整合。”长期与德方接触的陈明敏锐地意识到,这将是继蒸汽机、电机、计算机之后,“人类的第四次工业革命”。2014年10月,他吸收工业4.0理念,与德国合作伙伴在嘉定建起了国内首座工业4.0智能工厂实验室。
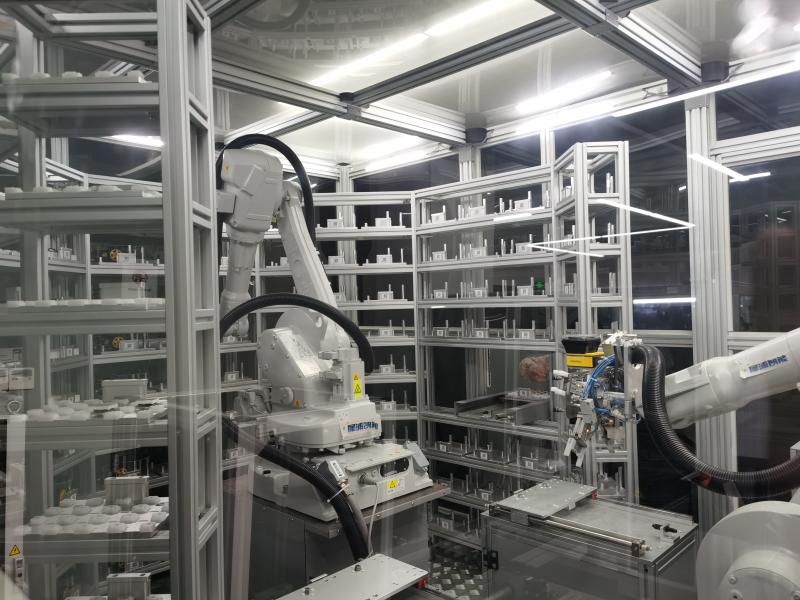
实验室建成后,吸引了大量学界、业界人士及政府人员参观。不久,当时的临港管委会也找上了陈明,希望他能在临港建设一个新的实验室。陈明很快答应,他觉得,临港定位上海智能制造产业中心,有丰富的应用场景与上下游企业;临港还布局了与工业4.0息息相关的信息通信产业,未来可期。
“中国在传统工业上与世界先进制造业还存在差距,但在信息通信技术方面有更好的基础。”陈明说,“工业4.0为中国提供了更好的弯道赶超机会。人才与技术密集的临港新片区,拥有更多的机会。”
搬来临港后,同济大学工业4.0学习工厂成为了展示工业4.0技术的橱窗。作为未来特定生产过程的展示场所,学习工厂让临港新片区的众多企业有机会学习、观摩并更好地适应工业4.0的发展。陈明说,学习工厂打算与临港新片区的企业在技术上合作,为企业研发试验新技术;研究与生产对接,也将让学习工厂更好地实现技术的更新和持续改进。
学习工厂还将为企业提供量身定制的在职人员培训。“产业会转型升级,工业4.0也可能在未来某日落后。”陈明说,“但只要人才紧跟着升级自己的能力,就总能适应新的时代。”